New BIG KAISER Angle Heads Combine Operations, Improving Accuracy, Increasing Productivity
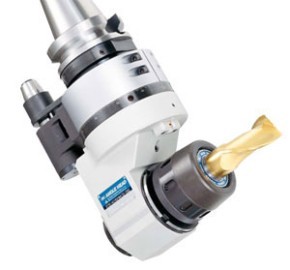
ELK GROVE VILLAGE, IL - New BIG KAISER Angle Heads combine vertical, horizontal and angular operations on one machine, improving runout accuracy and eliminating the potential for error created by multiple setups. They increase productivity by easily changing the angle of the cutter without repositioning the workpiece.
BIG KAISER Angle Heads feature superior quality components. They are equipped with hardened and ground chrome-nickel steel spiral bevel gears, super precision hardened and ground spindles, and high precision angular contact ball bearings.
A compact design assures rigidity and minimizes overhang, shortening projection length and reducing overall load. Minimized overhang also helps eliminate interference with the automatic tool changer (ATC) and connecting storage pockets in the tool magazine.
Universal Type Angle Heads (AGU series) are offered for machining all angles from 0 to 90 degrees with only one set-up. Angles are easily adjusted and precisely set at 1 degree increments with a positive locating system. Models for 40 taper machines offer up to ½” collet capacity and run at speeds up to 6,000 RPM. 50 taper models offer up to ¾” collet capacity and run at speeds up to 4,000 RPM.
90 degree (AG90 series) Angle Heads offer fixed 90 degree angle in a variety of tapers, lengths and collet capacities (.010" to .787"), using BIG KAISER’s new high precision Baby Chuck system. A Twin Angle Head provides two cutter heads 180 degrees apart, fixed at 90 degrees. AG90 Angle Heads offer speeds from 3,000 to 8,000 RPM.
In the AG90 series, HMC Type Angle Heads offer the combination of power and large diameter tool capacity, using BIG KAISER’s Hi-Power Milling Chuck system. Available in CV and BT 50 taper models, the HMC type Angle Head has a maximum speed of 3,000 RPM and tool diameter of 1¼”. This model is offered as High Rigidity "S” Type made with a steel housing and reinforced locating pin for applications that require heavier cutting loads.
Build-Up Type Angle Heads can be fitted with a wide range of 35 taper adapters to cover most machining requirements. Adapters are available for end mills, shell mills, slitting saws, drills, and tapping attachments.
BIG KAISER Angle Heads use an advanced non-contact sealing method that prevents coolant and particle contamination. A unique coolant jacket allows coolant coming through the stop block to be efficiently directed to the tool cutting edge while simultaneously cooling the Angle Head.
Simultaneous dual contact between the machine spindle face and the tool holder flange face and the machine spindle taper and tool holder taper shank is also available, using the BIG PLUS Spindle System. Simultaneous spindle and flange contact greatly enhances rigidity and repeatability, which yields many benefits in higher metal removal rates, higher accuracy, improved surface finish, and extended tool life. The BIG PLUS System’s increased rigidity assures the utmost performance of the Angle Head, resulting in more powerful machining.
BIG KAISER Precision Tooling, based in the Chicago suburb of Elk Grove Village, is the exclusive sales and marketing arm in North America for Heinz Kaiser, AG, Rümlang, Switzerland, a worldwide developer and manufacturer of precision boring tools of unmatched quality for thousands of applications in metalworking. BIG KAISER is owned by BIG Daishowa Seiki, one of the world’s leading producers of precision tool holders and measuring accessories.
BIG KAISER is a market leader in the development, manufacture and distribution of high precision boring tools, precision tool holders including BIG PLUS systems, modular tooling systems, carbide and indexable drills and endmills, precision tool measurement and presetting systems, workholding systems and machine accessories.
Did you find this interesting or helpful? Let us know what you think by adding your comments or questions below.